1. CAN I INSTALL A PARQUET FLOOR IN THE BATHROOM OR KITCHEN?
Wooden floors can be laid with no problems in both the kitchen and the bathroom. Water does not damage parquet floors as long as it does not stagnate. It is extremely useful to choose species of wood that are more stable in contact with humidity, such as Doussiè, Merbau, Iroko and Teak. Oak, on the other hand, requires certain precautions because it has a tendency to form blackish spots when it is exposed to humidity; the spots are caused by leaks of tannin, which is quite common in this type of wood.
Especially with the bathroom, it is important to consider carefully the type of parquet floor to be installed (size, type of wood and protection), taking into account your expectations and future use. If you expect that your bathroom will be used all the time, as it is the main bathroom in the house where family members wash themselves frequently and children also use it, it is important to guarantee the surface of the parquet floor with intense protection. In any case, for peace of mind and only as far as the shower, bathtub, toilet and bidet areas, it is recommended to choose more practical floor, made of stone or ceramic material.
In any case it is advisable, in order to have a good care of the floors, to always open the windows and aerate the rooms after the use of showers or alike, in order to remove possible humidity deposits in the rooms, and in this way avoiding the floors being altered.
2. WHAT ARE THE MAIN TECHNICAL CHARACTERISTICS AND BEST QUALITIES OF PARQUET FLOORS?
Extremely beautiful to look at, long-lasting and resistant to wear, good performances in case of mechanical and vibrational stress, excellent thermal and acoustic insulation: these are the most important qualities of a wooden floor. Other properties include resistance to being walked on, thanks to the intrinsic hardness of wood and the excellent elasticity that makes parquet especially suited for sports facilities. We also need to take into account that parquet floors last in time, along with the possibility to easily restore or renew them, through sanding or polishing.
Last but not least, the wood floor represents a choice that respect the environment, being an absolutely sustainable material, as it is a product entirely recyclable comparing to the laminated, ceramics, marble and similar products.
3. WHAT IS THE DIFFERENCE BETWEEN PARQUET AND LAMPARQUET?
The term “parquet” stands for the product in general, which is then subdivided into different types: “traditional” parquet in solid wood, “pre-finished” parquet, consisting of only one part in hardwood, etc. Lamparquet, on the other hand, is a type of floor with thickness from 8 to 10 mm, length from 250 to 300 mm and width from 45 to 65 mm. These dimensions are determined by Standard UNI 4375.
4. IS IT BETTER TO USE AN OIL-BASED FINISH OR A VARNISH-BASED ONE?
The choice of finish is very subjective: it depends on the final look and the feeling that one wishes to obtain from the wooden floor. The oil finish makes wooden floors look extremely natural, while the varnish finish highlights and enhances the shades and chromatic nuances of wood tissues. Aside from appearance, however, the finish also has to guarantee the functional performances of a parquet floor. Generally speaking, since oil finishes require more care and maintenance, people often opt for varnish finishes.
5. WHAT ARE LAMINATED AND MELAMINE FLOORS?
Laminated floors have nothing to do with wooden parquet floors. Made with wooden dust combined with other materials that make the floor look like a traditional parquet, they have quite different mechanical properties: they are less resistant and shorter-lasting.
A comparison carried out with the most noble and precious parquets is improper, to say the least, as these products are in fact synthetic. Synthetic floors are not parquets but rather facings of the decorative type that take advantage of the melamine resins applied to their exposed surface.
Made with supporting materials derived from wood (chipboard – MDF – HDF) they too are sensitive to significant changes in environmental humidity.
Their resistance to wear is certainly greater compared to wooden surfaces, but it could never be justified for normal use in homes, which also need qualitative requirements that only wood, with its natural and genuine nature, can offer. It helps to remember that a wooden surface is even more resistant than a ceramic one as the latter, in case of impact with a hard body, chips or breaks into two parts, but it will certainly not be dented, thus exposing itself to a minor damage.
6. WHAT IS MDF?
MDF is the laminate structure. MDF (Medium Density Fibreboard) is an engineered wood product, a panel in medium density fibre produced by a dry method, normally made using adhesive urea formaldehyde based. MDF, which is very widespread, belongs to the family of the “Fibre Panels”, subdivided in three distinctive categories, depending on the method used and the density: low (LDF), medium (MDF) and high (HDF)
7. WHEN A CHAIR WITH WHEELS LEAVES TRACKS ON THE PARQUET, IS IT BECAUSE THE VARNISH FINISH IS DEFECTIVE?
Absolutely not. It is the mechanical action of the wheels that, by changing the perfect planar surface of the varnish film, makes small indentations visible only against the light. To avoid further damage, simply replace the wheels with special rubber-coated wheels, more elastic than the varnish and consequently less damaging. This is nevertheless a feature specific to wooden floors and its physical characteristics to change in time; this is why it must be used and “lived” without any exaggerated or conditioning functional prejudices.
8. CAN PARQUET FLOORS BE LAID ON TOP OF PRE-EXISTING FLOORS?
Yes, if we are talking about floors which are solidly fixed, such as tiles, ceramic, marble or its by-products, and stone. The parquet floor can be laid after verifying the existence of all requirements for perfect foundations. Carpeting, PVC and linoleum, on the other hand, are incompatible with parquet, consequently they should be removed together with any trace of the old adhesive.
9. CAN PARQUET FLOORS BE LAID ON TOP OF CERAMIC TILE
Yes, you can install parquet floors directly on top of a ceramic one. However, you need to first remove all residues of wax, dirt or grease that may have deposited in time. Even minimum amounts of wax, dirt or grease may prevent the effective gluing of the parquet. Furthermore, it is recommended to smooth out the ceramic tiles, so that the fixing and securing properties of the glue may be further enhanced.
10. CAN SPECIFIC MEASURES BE APPLIED IN ORDER TO REDUCE NOISE?
The answer depends on the type of location taken into consideration.
In the case of a new house, and therefore still under construction, it is the responsibility of the industrial designer and the builder to follow the legislation in force for breaking-down the acoustic pollution.
In the hypothesis in which, there is the need to improve the acoustic insulation of a house already inhabited, the solution to adopt is to verify on a case by case basis (in the scenario of a floating lay it is provided with a layer of thermo-acoustic insulation).
11. HOW MANY TIMES CAN PRE-FINISHED PARQUET BE SANDED?
A pre-finished parquet can tolerate 2/3 sanding jobs, also called freshening up. In case you proceed with a sanding before the floor is already worn or damaged, and consequently before there are any deep carvings or indentations, you can sand the floor three or four times. However, the hardwood surface layer of the pre-finished cannot be less than 2.5 mm thick.
12. HOW MANY TIMES CAN TRADITIONAL PARQUET BE SANDED?
A traditional parquet floor can be sanded 2/3 times in exactly the same way as pre-finished parquet, since the total thickness of a 14 mm MF board of traditional parquet is generally the same thickness as the hardwood surface layer of a pre-finished material.
However, you need to consider that the varnish on the pre-finished has a higher hardness and resistance compared to the varnish applied during the laying of traditional parquet and therefore take even greater care over the procedure; remember that it is an extraordinary maintenance operation which should be carried out by skilled staff.
13. IS THE PARQUET SUITABLE FOR THE UNDERFLOOR HEATING SYSTEM?
When we talk about underfloor heating, the choice of using the wood is the best one considering that the parquet, being a natural insulation material, does not allow the direct contact with the heat coming from the radiant panels, hence allowing a constant and “silent” heat transfer.
All the pre-finished floors are suitable for laying onto a floor that has an underfloor heating, because it is provided with a multilayer support carved in more parts, supplying an even temperature throughout.
14. THE PRE-FINISHED ENGINEERED WOODEN FLOOR, BESIDES BEING SUITABLE FOR THE HEATING FLOOR SYSTEM, IS IT APPROPRIATE FOR THE COOLING FLOOR SYSTEM TOO?
Yes. The prefinished parquet can be lay without problems on the cooling screed, given that the wood inhibits the humidity and redress changes.
Generally the heating and cooling floor systems have the same plant and are regulated by the same reference Standard. An important remark is that these plants are ever-evolving. For this reason it’s very important to pay attention to the planning of the heat engineering of the subfloor and wood flooring system, that will have to meet the following requirements:
- to guarantee an appropriate thermal exchange with the area to heat, allowing energy savings foreseen by the system;
- to keep a suitable environmental temperature in case of climatic variations and when the plant in working.
It’s important to assure that the plant is fuctioning, in order to avoid any problem in the heating or refrigeranting coils, starting with the heating or refrigerating complete cycle, following the relative instructions, before the installation.
15. AN INSTALLER HAS INCORRECTLY USED THE ALCOHOL CAUSING SPOTS ON THE FLOOR SURFACE: WHAT IS NECESSARY TO DO IN ORDER TO REPAIR THE DAMAGE?
An important preliminary remark is the following: as soon as the wooden floor is installed, it’s absolutely recommended to remove immediately the glue spots, without waiting the end of the installation works and without rubbing the floor surface.
In fact when the glue, after its catalysation, is removed by rubbing the floor surface, it releases always shiny spots, caused by a chemical reaction.
In case the wooden floor surface presents these shiny spots, the best procedure is to sand slightly the lacquered surface and to re-lacquer it.
16. È CAN PARQUET BE CLEANED WITH ALCOHOL?
The use of alcohol for cleaning parquet is a rather delicate matter. It is very important to take special care over the concentration of the alcohol, since rubbing the wooden floor with alcohol may attack the varnish of the parquet, damaging it beyond repair. We recommend use of only the minimal amount of alcohol needed to remove the grease from the surface of the floor, to avoid causing damage.
17. UNSIGHTLY WHITE POWDER RESIDUALS HAVE SETTLED IN THE VAINS OF THE BRUSHING. WHAT COULD HAVE CAUSED IT? HOW CAN THIS PROBLEM BE SOLVED?
Very probably, the problem is due to the powder from the construction site.
Although some jobs are carried out in other areas, the powders of paintings, plasterboards and similar materials are volatile, and they can spread around far more easily than we think.
The chalk powders solidify once in contact with water: and while trying to clean it, the problem just turns out to be worse than before.
The correct way to behave when there are jobs to do in the house, where there is an brushed finish floor, is to cover the entire area throughout the duration of the jobs, so to avoid powders settling on the surface and on the distinctive lines featuring this type of floor.
If the problem above mentioned occurs frequently, the solution is to use a specific natural oily additive (B074); this must be used by skilled personnel. The additive B074 can be ordered at all our sales points.
18. HOW LONG CAN A PARQUET FLOOR LAST?
In a regular home, with 4 or 5 dwellers, parquet floors can last more than a hundred years. To this end and as proof of this, we remind you that in certain historical buildings there are ancient floors, wax-treated and with no varnish, that are still acceptable.
19. ARE PARQUET FLOORS EASILY DAMAGED?
A parquet floor can be very tough, bearing in mind that it is protected by a strong varnish, provided it is used and treated with due care. What should I do to avoid damaging the parquet? Any action which may damage the surface of the wood floor should be avoided. Examples include rubbing the surface of the parquet, dropping pointed objects onto it, allowing water to stand on it and walking over it in high-heeled shoes. Pets’ claws may also cause damage.
In the case of parquet, the part most subject to wear over the years is the finishing layer, which should therefore be conserved through thorough, regular cleaning and routine maintenance over time.
20. WHICH IS BETTER, FLOATING INSTALLATION OR INSTALLATION BY GLUING?
The laying method you choose for your parquet depends on the specific conditions of the location where the new wood floor is to be installed.
Often, the floating-floor type is better when you want to keep the existing floor or, in any case, you do not want to damage it.
Installation by gluing, on the other hand, is certainly better for guaranteeing stability in time, as the wooden boards are secured and glued. In the case of floating installations, the wooden boards simply rest on the floor underneath and are not secured or constrained in any way; this means that, as the temperature changes, but especially as the environmental humidity changes, they are more prone to deformation or cracking.
When it comes to care procedures over and above routine cleaning, we urge extreme caution when choosing and using products, to avoid damaging the parquet and avoid the risk of impairing the wood’s natural appearance.
21. THERE IS A DENT IN THE PARQUET: WHAT CAN I DO TO FIX IT?
In case of pre-finished parquet, you can simply replace the damaged board. On the other hand, if the parquet is the traditional type you have to proceed with sanding the entire floor surface, not only the dented part. The localized repair on a single board through sanding is possible only if the parquet floor has an oil finish. In case of varnish finish, you need to treat and re-varnish the entire floor.
22. WHAT PRECAUTIONS CAN I TAKE FOR THE MAINTENANCE OF PARQUET FLOORS? CAN I USE STORE-BOUGHT PRODUCTS?
For best floor maintenance, it is recommended to clean it constantly. In order to properly revive the varnish, it is important to use suitable waxing products, recommended and sold directly by the manufacturer.When it comes to care procedures over and above routine cleaning, we urge extreme caution when choosing and using products, to avoid damaging the parquet and avoid the risk of impairing the wood’s natural appearance.
23. HOW IS IT POSSIBLE TO VERIFY THE COMPLIANCE OF THE MATERIAL DELIVERED AGAINST THE MATERIAL ORDERED?
In order to protect both of the image of the Company and the interests of the Client, Berti is always available for a verification of all the material sent at time of delivery. In this way avoiding at start any problem that could possibly arise, verifying in person together with our shippers, the exact compliance of the material ordered against the material actually delivered.
Our service is not limited to the sale of the parquet. We wish to be sure that the customer has received the material requested and can go ahead with laying the wood floor without any difficulty.
1. HOW DO YOU MAKE THE ORDINARY MAINTENANCE OF VARNISHED FLOORS
All kinds of parquet are very easy to maintain. Parquet does not require any particular care, since all things considered it is a durable type of floor covering.
The varnished floor has received a protective surface treatment which, if well looked after, will remain intact for a long time, protecting the wood from wear and dirt, and will retain its characteristics and beauty over time.
A few simple rules should be followed to keep a parquet floor looking good over time:
- Place a doormat at the entrance to your home, to wipe the soles of shoes and remove dust or particles which may be abrasive on contact with the surface of the wood;
- Remove the dust that deposits every day with dust-grabber cloths, a fringed brush or a vacuum cleaner;
- Clean the parquet with a damp, well wrung cloth from time to time. A few drops of neutral parquet cleaner can be added to the water;
- Do not forget to perform regular treatments with protective products – which may be self-polishing or re-polishing – consisting of resins dispersed in water. The frequency of treatment will depend on the level of use and foot traffic on the floor.
- Always fit felt pads under the legs of chairs.
- Do not wet.
- Floors subjected to particularly heavy use may be protected with a special POLISH for pre-finished parquet.
- Do not use alcohol, ammonia or solvents which may damage the varnish.
These procedures, alternating with polishing even without using specific products, are sufficient to ensure hygiene and keep the floor in good condition over time.Questo tipo di accorgimenti, alternati ad una lucidatura anche senza l’impiego di prodotti particolari, è sufficiente a garantire igiene e conservazione nel tempo.
2. WHAT IS THE EXTRAORDINARY MAINTENANCE OF VARNISHED FLOORS?
In a parquet floor, what may deteriorate over time is the surface layer of varnish. Normally, in the areas subjected to greatest wear, the varnish tends to show signs of damage after 6-8 years. In this case, a parquet specialist must be called in to remove the worn layer and revarnish the whole floor. For more serious damage, a thicker layer will have to be removed (about 0.2-0.3 mm). After these operations, the parquet is normally as good as new. One advantage of parquet floors is that if they are properly treated and receive regular maintenance, they are virtually indestructible.
Other floor restyling procedures may be, depending on circumstances:
- replacement of the most seriously damaged elements;
- resanding;
- careful application of filler (on single cracks);
- sand-papering (for small scratches).
In exceptional cases, deep resanding may be needed; this will not be required until the floor is 10-15 years old. This procedure is possible up to 7-8 times on traditional parquet and 2-3 times on prefinished parquet.
3. WHAT DOES SANDING PARQUET MEAN?
Parquet needs sanding whenever signs of wear such as scratches or stains cannot be removed by ordinary polishing. It is usually carried out every 7/8 years, since it is an extraordinary maintenance procedure on both pre-finished and traditional parquet.In practice, sanding the parquet removes a few tenths of a mm from its surface layer.This procedure has to be carried out by skilled staff with the right equipment. Poor sanding might damage the parquet floor beyond repair, causing marks which cannot be removed by the finishing operations which follow.
4. WHICH IS THE ROUTINE MAINTENANCE OF WAX-TREATED FLOORS?
In order to preserve the beauty of a wax-treated floor, it is important to carry out a few simple steps:
- Put a doormat outside the main entrance in order to remove dust or fleck of dust from the bottom of shoes that may be abrasive in contact with the wooden surface;
- Remove dust, even by using a vacuum cleaner;
- Every once in a while, clean the parquet with a dampened and well-wrung cloth. To dampen the cloth, in addition to water you can also add a few drops of neutral detergent specific for wooden floors;
- Eliminate stains or any traces of skid marks caused by rubber soles using the specific solvent for wax-treated floors;
- Periodically polish the floor.
Every once in a while, we also recommend re-polishing the floor, after having applied a thin layer of liquid wax to the entire surface.
5. WHAT IS THE EXTRAORDINARY MAINTENANCE OF WAX-TREATED FLOORS?
Extraordinary maintenance of wax-treated floors consists in a new application of wax, to be done only after having cleaned the entire surface with a cloth dampened with wax-based solvent. After applying the wax, proceed with the traditional polishing.It is suggested to make use of the support of qualified personnel to proceed with such maintenance.
6. WHAT IS THE MAINTENANCE OF OIL-TREATED FLOORS?
Oil-treated floors should be cleaned exactly like the varnished floors. At a later time, and in compliance with the manufacturer’s instruction, liquid wax for oil-treated floors should be applied. Then, the floor can be polished with a polishing machine or with a cloth made of natural fibres.
It is suggested to make use of the support of qualified personnel to proceed with such maintenance.
11. WHAT IS THE SOLID WOODEN FLOOR?
The solid wooden floor is made of hardwood elements. The elements that form the solid wooden floor must have the four flat edges perpendicular to the face with maximum tilt between 0° and 3°.
2. WHAT IS THE PRE-FINISHED MULTILAYERS FLOOR?
The name pre-finished engineered multi-layers floor is generally used to describe a series of wooden elements consisting of different layers, with tongue and groove joint on the sides and previously calibrated, sanded and lacquered before the installation. Highly innovative, the pre-finished floor consists of a valuable hardwood top layer that can be walked on and of a support, whose task is to hinder deformations due to the natural wood settlements and ensure extremely high resistance and hardness properties. The top quality of the processing and the specific surface finish, which is carried out through an industrial application of the lacquer, guarantee the product hardness, durability in time and waterproofing, in addition to very fast installation. Last but not least, the great beauty and extremely natural effect of pre-finished wooden floor make it a truly prestigious floor.
3. WHAT IS THE DIFFERENCE BETWEEN SOLID AND PRE-FINISHED WOODEN FLOOR?
Per “parquet monostrato” o “tradizionale” si intende un pavimento realizzato con elementi costituiti da un unico strato dello stessa specie legnosa. Il “parquet stratificato” o “prefinito” è invece la pavimentazione costituita da elementi multistrato, ossia composti da due o più strati di legno diverso, di cui quello di calpestio o nobile realizzato in legno massiccio. Per parlare di “parquet”, lo strato nobile del pavimento deve avere uno spessore non inferiore a 2,5 millimetri.
As “single-layer ” or “solid wood” is intended a floor consisting of only one layer of the same wood species.
The “multi-layers” or “pre-finished” engineered floor, on the other hand, is a type of wooden floor consisting of multi-layer elements made up of two or more layers of different wood species, including the hardwood top layer that can be walked on.
Finally we can talk about “wooden floor” when the hardwood top layer is at least 2,5 mm thick.
4. WOODEN FLOORS: TYPES AND EXPLANATIONS
The traditional parquet sizes include:
Maxilistone: Thickness 24 mm | Width from 100 to 140 mm | Length from 800 to 2000 mm
Lamparquet: Thickness from 8 to 10 mm | Width from 45 a 60 mm | Length from 250 to 300 mm
Listoncino MF: Thickness from 14 to 15 mm | Width from 75 a 90 mm | Length from 500 to 900 mm
Listone MF: Thickness 22 mm | Width from 80 to 100 mm | Length from 600 to 120 0mm
5. PRE-FINISHED WOODEN FLOOR: SIZES AND DIMENSIONS
As far as it concerns the counterbalancing, Berti decided to make the pre-finished floor more stable, applying to the top wood surface layer a crossed multi-layer birch wood support. The birch wood is a more valuable material comparing to the average and this is the reason why we have chosen this type of wood.
6. HARDNESS AND DIMENSIONAL STABILITY
The hardness of wood indicates its resistance to penetration of the element load placed on a face of the element (said screen test). It is determined by following the procedures and instructions set out by standard UNI EN 1534 – Determination of resistance to penetration (Brinnell).The Brinnell hardness is determined by the entity of the load mark identified in the wood. Less is the entity of the mark, more is the hardness of the wood, and therefore more resistant and enduring is the floor.It is important to consider that the wood is a “live” material and its structure, shaped by nature in the course of the years, is not consistent: for this reason the screen test Brinnell is performed various times in each type of wood. Dimensional stability, on the other hand, indicates the changes in wood volume as environmental humidity and temperature values change. Dimensional stability is calculated by applying the test method established by standard UNI EN 1910 – Determination of dimensional stability.
7. WHAT IS THE LAYING GEOMETRY?
The laying geometry is the pattern created by the positioning of the individual elements that make up a wooden floor. The final result depends on several factors: size of the wooden pieces, choice of geometric or non-geometric mosaics, creativity in combining elements. The reference standard that specifies the main and most common laying geometries is UNI EN 13756 – Wood flooring – Terminology.
IRREGULAR BRIDGE DECK OR SHIP’S DECK OR RUNNING
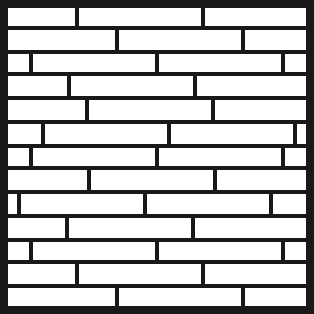
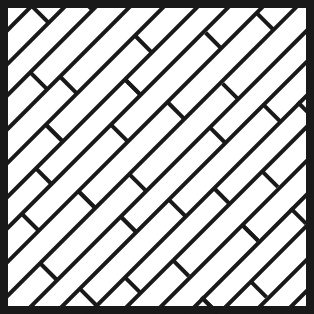
The pieces, of equal size, are arranged so that the head joints are in the same centre line, or in any case in a constant position compared to each strip that makes up the previous row. This means that the parquet is laid in a regular, symmetrical pattern.
In irregular bridge deck laying, also known as ship’s deck or running laying, the wooden strips have the same width but random length. The resulting effect creates a floor with an unsymmetrical, original look.
FASCIA E BINDELLO (BAND AND CONNECTING ELEMENT)
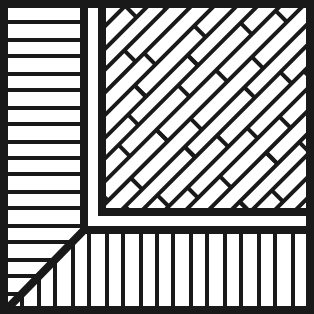
This is the finish of the floor perimeter. It consists of wooden pieces with a different laying pattern (fascia) compared to the predominant pattern (central rug) and of other pieces positioned as a connection element (bindello) between the different laying patterns. In this parquet laying pattern, different colours can be used for the band and the connection element, to highlight the different parts of the floor.
HERRINGBONE LAYING
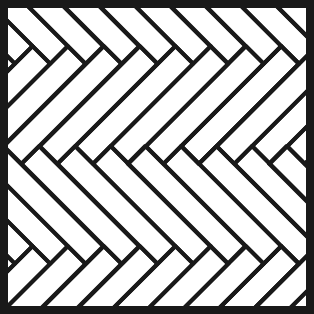
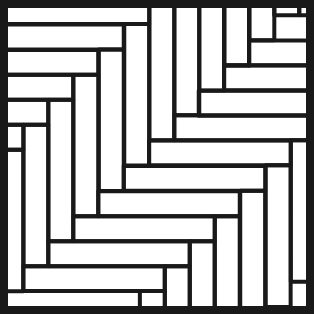
The pieces, rectangular in shape and of equal size, are laid at a 45-degree angle with respect to the walls. The pattern of the parquet resembles the bones of a fish; hence the name.
HUNGARIAN HERRINGBONESPINA UNGHEREE
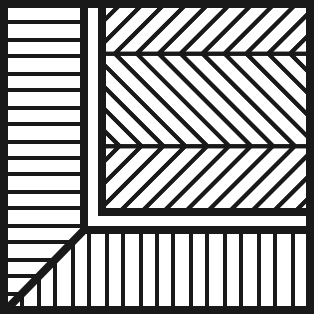
Each individual piece has two short sides cut with a 45-degree or 60-degree inclination with respect to the long sides. The laying method is the same as the herringbone laying. Here again, different timbers can be used to highlight the two areas of the floor.
8. THE FINISH
The finish is the treatment of the surfaces of semi-finished parquet using varnish or an penetrating sealer. Used to protect, customize the colour or enhance the decorative characteristics of the selected wood species, it also indicates the calibration and sanding operations carried out before the aforementioned treatments.
WAX TREATMENT: Waxes used on wooden floors are made with synthetic and natural waxes, mainly dissolved in mixtures of solvents or dispersed in water. Available in the form of more or less viscous pastes, or in fluid dispersions, they are see-through or slightly coloured to provide special nuances or shades to the treated wood.
The main feature of a wax treatment is that it does not form a uniform film over the surface of the wood, respecting its natural look. This treatment offers limited protection, consequently it has to be repeated in time.
OIL TREATMENT. Oils used to treat wooden floors consist of mixtures of natural drying oils, mixed with waxes and resins of a various nature. Usually dissolved in organic solvents, they can also be dispersed in water. Their hardening occurs through both the evaporation of solvents and through a chemical reaction with the oxygen in the atmosphere, and it is generally accelerated by using suitable additives made with metallic salts.
The oil treatment does not form a film on the surface but instead causes a sort of impregnation of the wood, respecting and enhancing its natural appearance.
9. WHAT SHOULD BE THE HUMIDITY LEVEL OF A WOODEN FLOOR AT THE MOMENT OF THE DELIVERY?
The humidity level of a parquet floor on delivery is a very important parameter, for which formal standards are set. The law requires a humidity level between 7% and 11%.
At Berti, the drying procedure used on the hardwood layer of pre-finished parquets produces strips with a humidity percentage of 6/8%. The humidity level of the plywood is 10/12%. When pre-finished parquet is pressed to obtain the product sold to our customers, a stabilisation process takes place, providing humidity percentages which compensate each other and stabilise at levels up to the 10% threshold. No Berti products ever exceed a humidity percentage of 10%.
This guarantees an excellent quality product.
10. HUMIDITY AND WOOD REACTIONS
The wood has dimensional characteristics that depend on its hygrometric layer, that is its humidity level, which in turn depend on the environmental conditions where it is stored.
In fact, it has been proven that temperatures over 22 degrees and environmental humidity below 45% can cause unsightly deformations in the wood that, in the most serious cases, may even cause certain parts detachement.
Optimal conditions for perfect maintenance of the properties of parquet floors are a temperature included between 18 and 21 degrees and a humidity percentage of the air included between 45% and 60%: this environmental hydrometric interval provides comfort and physical well-being to people living in the rooms, in addition to beauty and stability of the wooden floor.
11. SUITABLE FOUNDATIONS AND LAYING CONDITIONS
Parquet floors can be laid on top of a cement screen, on panels wood based, on pre-existing floors or on nailing strips.
The screed, which must be at least 40 mm thick, is made with regular or quick-setting cements. Drying times of regular cement vary from 4 to 7 months or longer, depending on the products used and on environmental conditions. The drying times of quick-setting cement, on the other hand, vary from 3 to 7 days: in this case, the humidity check must always be carried out using a carbide hygrometer. Whatever the case, regardless of the foundation time, it is required by law to apply polyethylene sheets folded over along the walls in order to create an effective vapour barrier.
If, on the other hand, the parquet floor is laid on top of pre-existing floors, it is important to make sure that these floors are in good condition, perfectly washed and grease-free, sandpapered in case of ceramic or marble floors or stuccoed in case of an old parquet floor. For carpeting or linoleum, after removing them it is recommended to eliminate any glue residue by carrying out a light sanding.
12. SCREEDS OVER UNDERFLOOR HEATING: WHAT IS THE PRE-HEAT CYCLE?
To stabilise and dry the screed effectively, after a proper seasoning, a preheating cycle is essential. As well as drying the screed, this procedure checks that its structure will withstand the highest possible stresses, ensuring that future thermal shocks will not damage the surface of the wood floor.
There are no disadvantages in using the pre-finished parquet on underfloor heating systems, however it is important to take into consideration that the wood floor is subject to shrinking and adjustments.
Before laying the wooden floor, it is essential to follow the listed solutions below, in order to execute the pre-heat cycle:
- Activate the underfloor heating system, gradually increasing the temperature up to 5°C per day until reaching the limit of 35°C (called operating temperature);
- Leave the system on at operating temperature for at least a week;
- After a week gradually decrease the temperature up to 5°C per day until reaching the power off of the underfloor heating system;
- Once completed the cycle, it is possible to start laying the parquet with the underfloor heating power off and its surface temperature around 18-20°C;
- Once the wood floor has been installed, it is possible to switch on the underfloor heating system: once again gradually increasing the temperature of 5°C per day;
- Never exceed the maximum limit of 30°C for the heating fluid;
- Remember that once the system is operating, the surface floor temperature must not exceed the 25°C.
13. WHAT IS THE MOST SUITABLE METHOD FOR LAYING ONTO A FLOOR THAT HAS AN UNDERFLOOR HEATING SYSTEM?
The most suitable choice in terms of laying method is the glue down installation, so not to allow air spaces between the screed and the parquet boards (which would cause a heat loss).
In the case of floating floor installation, it is appropriate to choose sheathings suitable for heat transfer.
It is important to remember that the wood is a natural thermal insulation material: therefore, it is advisable to lay parquet boards 16 mm thick, in order to have an efficient heat transfer.
È importante ricordare che il legno è un materiale isolante termico per natura: quindi come linea generale si consiglia di posare un parquet con uno spessore totale non superiore a 16 mm, per avere una trasmissione del calore efficace.
14. WHEN IS THE RIGHT TIME TO INSTALL A PARQUET FLOOR?
You can proceed with the installation at any time, as long as the foundation is compact and dry, with humidity of less than 1.5%. Also, all the door and window frames have to be assembled and fully operational, masonry jobs have to be completed and the electrical and hydraulic systems must be working perfectly. Room temperature cannot be lower than 10 degrees, and relative humidity of the air has to be included between 45 and 60%. The laying and polishing of adjacent floors, in ceramic or other material, must also be completed, along with the finishing and painting of ceilings and the preparation of walls.
15. TYPES OF LAYING TECHNIQUES
There are three main techniques for laying a wood floor, which also vary depending on whether the parquet being used is traditional or pre-finished:
FLOATING TECHNIQUE. Floating parquet floors consist in a single-piece wooden surface simply laid on top of the support surface: made with pieces equipped with joints, glued one to the other by means of vinyl glue and usually large in size, they consist of three layers. More in detail, a vapour barrier and a layer that may have various functions, the most important one being soundproofing, is positioned between the floor and the parquet. In case of an under-floor heating system, the insulating layer has to have low thermal resistance in order to allow proper heat radiation.
LAYING BY MEANS OF GLUE. On the laying surface, a suitable adhesive is applied using a special spatula with triangular teeth; the glue is applied with wide half-circle movements so as to obtain what is known as adhesive lines, allowing proper contact between the adhesive and the support. In fact, it is important for the glue to be applied evenly. Too much glue or not enough can jeopardize proper laying of the parquet and cause defects in the application. Unlike the floating technique, the side of the strips is not glued.
When using pre-finished parquet, it is important to choose the correct type of glue, to prevent warping of elements or incompatibility with the pre-varnished wood elements. Naturally, we cannot accept any responsibility in case of problems of this kind.
LAYING BY MEANS OF NAILS/SCREWS. This type of laying technique is typically used for multi-layer elements or solid elements with perimeter joint (large strips) and thickness of 14-15-22 mm. The elements are secured by means of nails or screws at a 45-degree angle, in the top part of the male and penetrating inside the support for at least 20 mm. This is why it is so important to choose the most suitable support, in order to provide for excellent fixing operation.
16. THE PRODUCT SHEET
All products sold and marketed on the domestic territory and intended for the final user have to have technical data sheets indicating, in the Italian language, clearly visible and legible information pertaining to:
a) product legal or trade name;
b) name or brand of the producer or importer established in the European Economic Community;
c) materials used for the structure and for the cladding;
d) presence, if any, of materials or substances toxic for man, objects or the environment;
e) product maintenance and cleaning instructions, possible precautions and intended use for the purpose of proper product use and safety;
f) product legal or trade name;
17. BERTI PRODUCTS GUARANTEE
The branded BERTI wood flooring collections, are manufactured with the best raw materials, following production standards using the most advanced technologies together with the experience and know-how of our skilled people. Every Berti wooden floor undergoes a series of thorough quality controls to meet the high standards that indentify Berti wood flooring.
All stages of the manufacturing process are carried out with care and accuracy to give the guarantee of a product that lasts over time. Berti products are eco-compatible: when you choose Berti, be sure to follow the principles of environmental protection. Berti’s values are the result of a mix of technology, aesthetics and design, respect for the environment, industrial processes and craftsmanship.
Berti Wooden Floors is synonymous of reliability: the company has been on the market for over 40 years.
Berti pre-finished engineered wooden floors are CE certified (reference standard EN 14342:2005 + AC:2008), they are subject to the strictest European standards for the environment and health. The products meet full satisfaction of the E1 class limits (re. UNI EN 717-1:2004 – equilibrium concentration of formaldehyde does not to exceed 0.1 ppm).
Berti wood flooring boasts a formaldehyde concentration of 0.01 ppm, which is much lower than the legal requirements and widely within the limits foreseen for class E1 products. All engineered wood flooring are classified as Cfl-S1 class, in full compliance with the limits of reaction to fire standard EN 13501-1: 2007.
In complementary work processing, such as UV lacquering or oiling and gluing operations there is no emission of solvents into the atmosphere thanks to the use of water-based lacquers.
Berti Wooden Floors has chosen to point out the environmental protection. This is why we use birch plywood support, exploiting not only its incomparable mechanical properties, but also its higher efficiency in terms of forest regeneration and environmental sustainability.
In the last year, Berti has adopted a series of measures for the health and safety protection of its workers to improve working conditions and reduce the likelihood of accidents.
18. COULD THE USE OF SCOTCH TAPE CAUSE SOME DAMAGES ON LACQUERED WOODEN FLOORS?
As written in our product data sheet that is supplied together with all Berti products: “During the installation of wooden floors do not use scotch tape on the floor in order to avoid damages on the finishing”. The bonding layer of adhesive tapes, which in most cases contains weak solvents that produce the typical layer of sticky tape, is responsible for a weakening of the lacquering. The lacquer on the wooden floor could be partially removed, taking away the scotch tape. For this reason it’s better to avoid applying scotch tape on parquet.
19. THE OXIDATION PHENOMENON
Oxidation is a completely natural phenomenon caused when the parquet is exposed to light. Its extent depends on the type of timber chosen, with varying degrees of change in the wood floor’s colour. Usually, oxidation is more noticeable in exotic timbers (such as Teak, Doussiè and Iroko). The wood generally becomes darker and its vein patterns more uniform. The speed and intensity of the oxidation depend on the brightness of the light to which the parquet is exposed and the finish applied (the use of different types of varnish may either enhance the colour and oxidation or limit it considerably). The duration of the oxidation process also varies; it may continue for several years, although it will be slower after the first few months.Once the furniture is moved, the parquet which has been in the shade will quickly turn the same colour as the parts exposed to the light.
20. HOW LONG DOES IT TAKE FOR A PARQUET FLOOR TO OXIDIZE?
Oxidation duration of parquet floors depend on the selected wood type.
Doussié, iroko, teak and afrormosia (African teak) oxidize faster.
Furthermore, during the oxidation process the amount of light is extremely important, and it is directly proportional to the oxidation speed.
In order to make the colour of parquet floors more even and warmer, we nevertheless recommend letting the entire surface oxidize thoroughly before you position rugs.
21. CERTIFICATIONS AND CE MARKING
The certification and CE marking must be affixed by whoever launches the product on the market, be it the manufacturer, in other words the one that materially manufactures the product, but also the company that imports or resells the product under its own brand and its own trade name. The latter, for labelling purposes, also becomes a manufacturer for all intents and purposes and it is consequently totally responsible for the brand and for the product.
In order to add the CE marking to a parquet floor, the manufacturer has to verify product conformity, adhering to a set of criteria and performance characteristics dictated by European Regulations.
The performance characteristics are:
- Durability in time
- Reaction to fire
- Release of formaldehyde
- Emission of pentachlorophenol
- Bending strength
- Slipperiness
- Thermal conductivity
22. WHAT IS FORMALDEHYDE?
Formaldehyde is a pollutant that is defined as ubiquitous, because it is found practically everywhere: in the city and along the road due to traffic, in homes and offices due to cigarette smoke, in furniture, since it is contained in chipboard, in plywood and in glues, and in foodstuffs, cosmetic products, packaging materials and glue used in books and magazines.
A law decree was issued on December 11, 2008 which enacted extremely strict rules concerning the manufacture, import and launch on the market of wood panels and artefacts, both semi-finished and finished products, containing formaldehyde. This includes wooden floors. According to this decree, companies cannot sell products whose equilibrium concentration of formaldehyde exceeds a value of 0.1 ppm (0.124 mg/m³), which corresponds to the limit set for class E1.
All Berti products respect the legislation provided by Law concerning the limits allowed for the formaldehyde concentration.
23. THERMAL CONDUCTIVITY
For parquet, resistance to thermal conductivity should not exceed about 0.17 mqK/W.
Thermal conductivity should be considered for ideal laying conditions, since the screed should comply with the best compactness and thermal conductivity criteria. This is particularly true in the case of floating floors, since the calculation of the element’s thermal conductivity may also contribute to the creation of any deformities such as size distortions, cracks and separation of the glued bond between the facing layer and the substrate.
The thermal insulation of a building is often underestimated. When designing a building, the choice of the most suitable insulation takes for granted an indicative knowledge of physics principles applied to construction. Here are some basic concepts.
The ability of a specific construction material to accumulate heat is calculated through its specific thermal capacity c (J/kgK); the greater this ability, the more the material is capable of accumulating heat.
Thermal conductivity l (W/mK), on the other hand, is the ability of a material to conduct heat. Coefficient I indicates the amount of heat that flows through one square meter of material 1 m thick, with a temperature difference between indoors and outdoors of 1 K (Kelvin degree). Insulating materials have a coefficient I of less than 0.1W/m*K.
Lastly, transmittance U (W/m²*K) represents the heat flow yielded by an indoor environment to the external air, through a surface area of 1 square meter and a temperature difference of 1K (Kelvin degree). When we talk about transmittance, we are referring to a stable condition, in other words constant indoor and outdoor temperatures. The smaller the coefficient U of a certain structural element the smaller the thermal dispersions and the better the insulation.Alcune nozioni di base. La capacità di accumulo del calore di un materiale da costruzione viene calcolata attraverso la sua capacità termica specifica c (J/kg*K): tanto è maggiore, tanto più il materiale è in grado di accumulare calore. La conduttività termica l (W/m*K) invece è la capacità di un materiale di condurre calore. Il coefficiente l indica la quantità di calore che fluisce attraverso 1 metro quadrato di materiale dello spessore di 1 metro, con una differenza di temperatura tra interno ed esterno di 1 K (grado Kelvin). I materiali isolanti sono caratterizzati da un coefficiente l minore di 0,1W/m*K.
24. PERIMETER AND EXPANSION JOINTS
It is recommended to avoid laying a parquet floor next to a rigid surface that may paralyse the natural movement of wooden elements. This is why it is so important to provide a expansion joint along the entire perimeter of the room, positioning shims in the starting phases and wedges in the closing ones. You can also use special clamps and straps. This operation should be carried out especially when large elements are being laid.
25. PARQUET FOR SPORTING FACILITIES
Flooring for sports facilities must meet high and guaranteed quality standards, with methodologies that work on elastic sub-constructions, so as to be suitable for any structure: gyms, sports halls, outdoor sports facilities, etc. in many variations but if you want to choose a sports parquet that meets the characteristics of professionalism, safety, durability, ease of restoration, reuse and with a low environmental impact, the most suitable choice to meet the needs of designers and end users is represented by parquet prefinished. Pre-finished parquet, in fact, allows you to achieve the best compromise between performance and safety, helping to maintain a healthy internal environment and at the same time free of static electricity. To offer optimal performance, sports flooring must possess certain general characteristics, listed below:
- Stability
- Uniform bending and oscillation
- Ultimate strength
- Controlled slipperiness
- Safety in case of falls
- Good thermal insulation
- Resistance to dirt
- Easy marking of the courts
- Non-deforming
- Low management costs
26. DECKING OR PARQUET FOR OUTDOORS
Decking or parquet for outdoor use, is perfect for paving terraces and gardens, swimming pool areas, gazebos, beach boardwalks. Remarkably resistant, it can be laid on top of existing floors and proves to be especially tough even when it comes in contact with the ground or with water. It does not require any special treatment: to prevent colour changes caused by constant exposure to the sun, special natural oils are used. Thanks to the knurl processing of the strips, decking is not slippery, even when it is wet. Thanks to its inherent characteristics of durability, hardness, flexibility, renewability and beauty, wood is the ideal material for outdoor floors, and the best solution in “extreme” environments that require specific technical performances. Teak, Iroko, Thermo-Treated Ash, Ipè and other wood species, especially South American ones, are commonly used for outdoor wooden floors.
27. WHAT IS THE CORRECT WAY TO VISUALLY EVALUATE A WOOD FLOOR?
The visual test of the floor is performed, as shown in the UNI CEN/TS 15717, observing the floor following the below procedure:
- Stand in an upright position;
- With the help of diffuse natural light, coming from behind the observer.
To identify and evaluate the presence of imperfections on the floor surface, sources of artificial light directly pointed to the floor, must not be used in any case.Per individuare e valutare la presenza di difettosità sulla superficie della pavimentazione in legno non devono in nessun caso essere utilizzate fonti di luce artificiale indirizzate direttamente sulla pavimentazione.
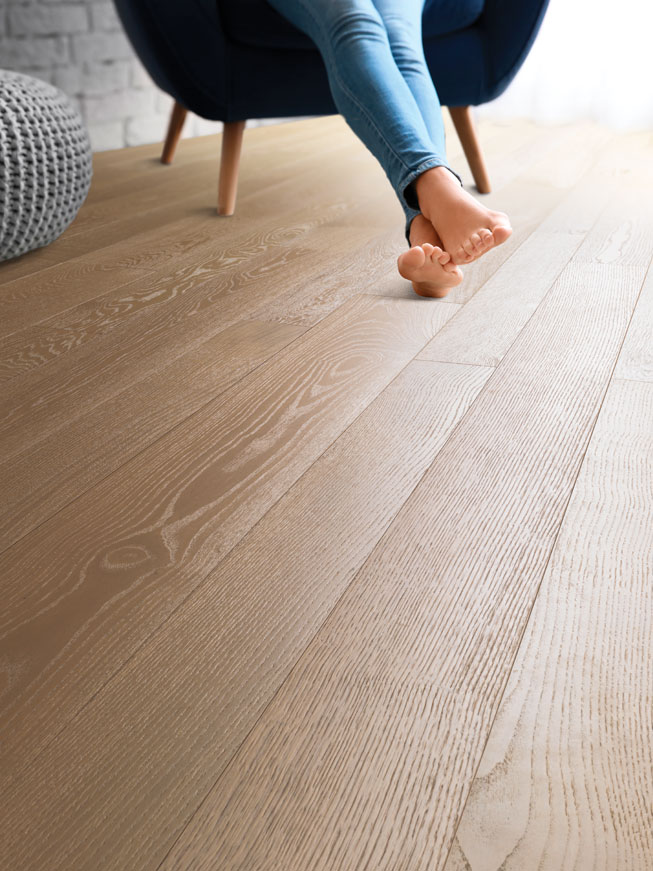
Do you need advice?
We will be happy to guide you, with all our experience, in the most suitable choice of parquet, floors, coverings and wooden stairs.
"*" indicates required fields